Fourth-year undergraduate student pursuing two B.S in Mechanical Engineering and Aerospace Engineering.
High Altitude Earth Exploration Prototype Vehicle
Undergraduate Aerospace Engineering course group project (01/2022-04/2022).
Project problem: Request from NASA to design, build and test a prototype hovercraft for a high-altitude Earth exploration vehicle that must quickly move across the surface.
University of Michigan course group members:
Daniela Mata, Assel Surshanova, Andre Jones, Carter Krumins, and Douglas Voigt.


Hovercraft System - PULLER Configuration
The final prototype uses a puller configuration to obtain higher maneuverability. Electrical and non-electrical hardware are included for reference.
Design Overview and Components
Hovercraft Electrical Hardware: These include the components shown in the image plus a lift motor, propulsion motor, control servo, and a power switch.
CAD Bullet Shell Design with skirt: Final bullet design chosen due to favorable aerodynamic results, modeled with CATIA.
Hovercraft Electric Hardware, Propeller, and Servo Mount: A propeller is mounted in a puller configuration for better maneuverability. A Servo motor was implemented to allow the propeller's rotation with respect to the shaft.
Impeller Design: Utilizes vanes to distribute the incoming air outward within the shell. It was 3D printed with PLA and had a mass of 26 grams.
Assembly: The different sections of the shell were laser cut on cardboard and assembled with tape and hot glue. The skirt was attached with tape, and the electrical and non-electrical hardware was attached with hot glue or tape.

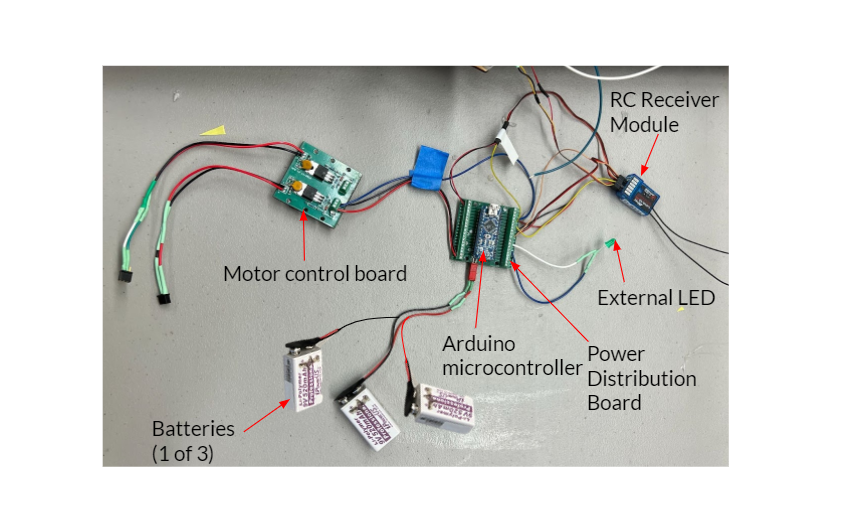
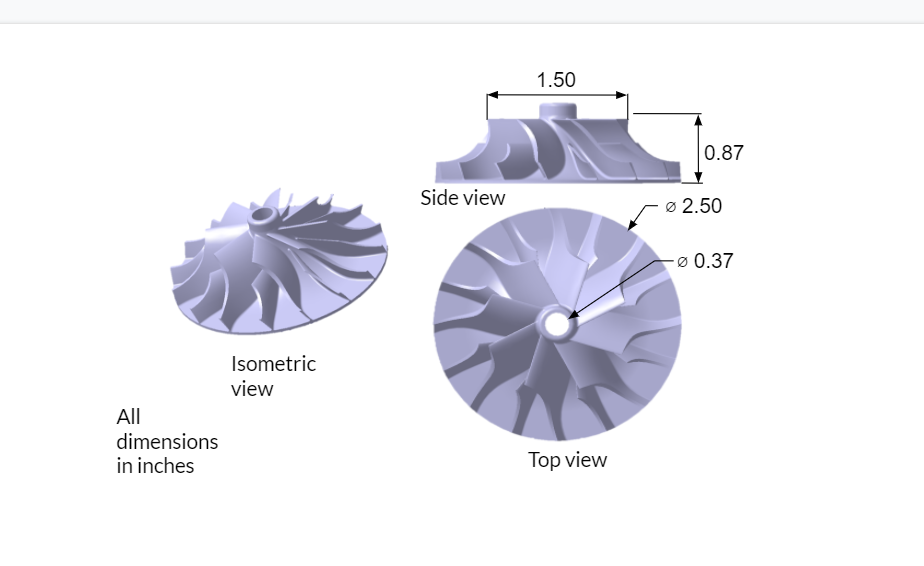

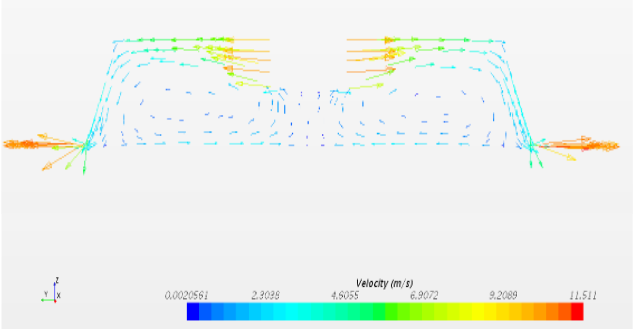


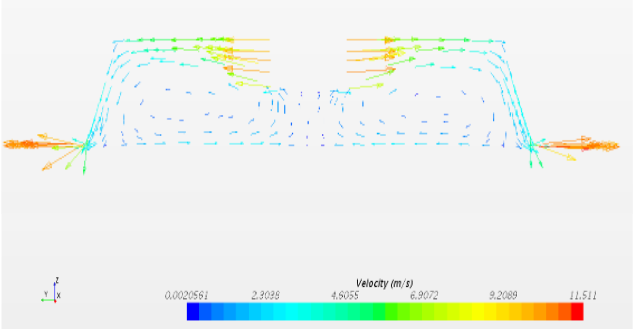
Final Analysis and results
Hovercraft's Simulated Fluid Flow:
Parameters:
Craft Altitude: 0.1"
Inlet radius: 1.72"
Shell Height: 2"
Inlet velocity: 5 m/s
Simulated Shell's lift with the Star CCM+ package:
The lift generated: ~6.5 N = 662 g (Can lift the system mass of 649 grams)
Power used: ~3.98W
Boundary conditions:
Bottom plate: Wall
Inlet Area: Velocity inlet
Outlet area: Pressure Outlet
Results:
Earth Prototype:
Bullet shape shell, 20” L x 13” W x 2” H
Shell mass: 160 g / System mass: 429g
Batteries: 3 / Power: 24W
Earth Prototype Components:
Skirt to increase lift & stability
Impeller optimizes airflow for increased lift
Propeller and servo for maneuverability
Multiple batteries for additional power requirements
Final Hovercraft Test
Previous to the course competition
The hovercraft moved at high speed with easy maneuverability while carrying a payload of 200 grams.
The skirt increased lift and stability.
Impeller optimized airflow for increased lift.
Propeller and servo for maneuverability.
Multiple batteries for additional power requirements.
Acknowledgement
Professor Washabaugh, University of Michigan.
Deven Parmar, AEROSP205 TA at the University of Michigan.